The polyester clean cloth industry in China started late, mainly after the 1980s. With the national industrial policy listing the electronic information industry as an important national development direction, the color TV, computer, communications, integrated circuit and other industries have entered rapid development At the same time, the introduction of a large amount of foreign investment puts forward new ultra-clean concepts and requirements for the microelectronics production environment, which has accelerated the rapid development of the industry.
In recent years, in the field of semiconductor integrated circuits, the state has provided support from tax incentives, investment approvals, equipment imports, land plants, etc., attracting a number of leading IC companies including Intel, TSMC, SMIC, and Samsung Semiconductor. Domestic investment in the establishment of factories and project expansion; in the field of pharmaceutical manufacturing, the implementation of the new version of GMP standards has greatly increased domestic pharmaceutical companies' demand for clean room and clean cloth product upgrades.
According to the '2019-2023 China Polyester Cleanliness Cloth Market Analysis and Development Prospects Research Report' by Xinsijie Industry Research Center, the domestic polyester cleanliness cloth industry market size reached 2.765 billion yuan in 2018.
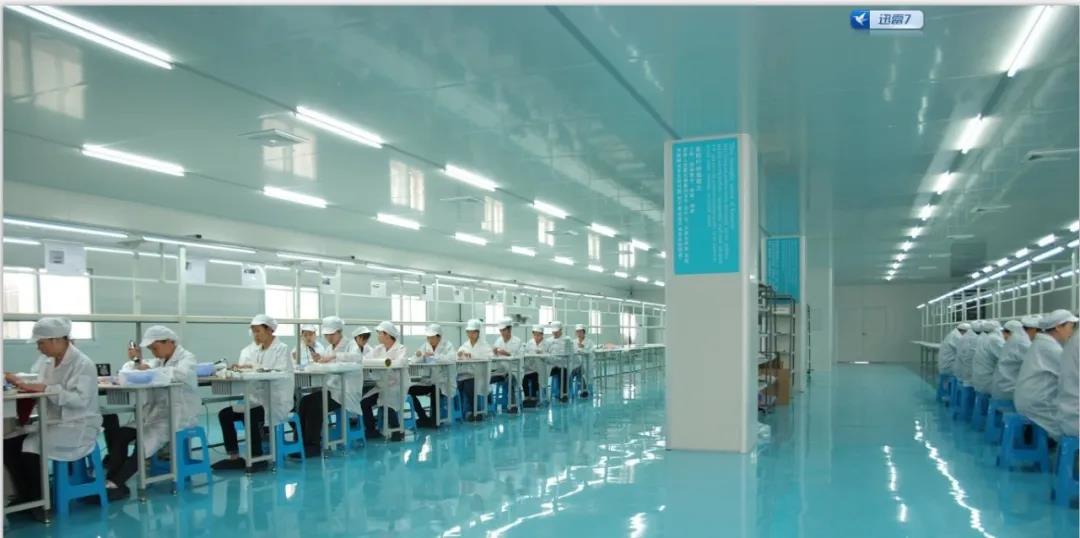
Application range of clean cloth
What are the main uses of clean cloth? Dust-free cloths are mainly used for wiping conductor production line chips, microprocessor assembly production lines, etc.; LCD liquid crystal display products and circuit board production lines, etc.; precision instruments, optical products, aviation industry, etc.
Because the dust-free cloth is made of 100% polyester fiber double woven, the fiber diameter is small, so its bending stiffness is small, the hand feel is particularly soft, it is easy to wipe sensitive surfaces, does not detach the fiber when rubbed, and has good water absorption and cleaning efficiency. Therefore, the application of dust-free cloth in these industries has a very obvious effect, and the dust-free cloth can be used repeatedly when it is properly cleaned.
Dust removal principle of microfiber clean cloth
A. Multiple scraping effects: A single thick single fiber can be ultra-fine to become hundreds of ultra-fine fibers, so when used as a cleaning cloth, the ultra-fine fibers can have more scraping effects than ordinary wipes .
B. The effect of wide contact area: The general fiber is thicker and has high bending rigidity, so the contact area between the fabric floating point and the object is small. On the contrary, the ultrafine fiber has small bending rigidity and soft (imitating silk), so the fabric floating point is in contact with the object. Large area and strong cleaning power.
C. Internal peeling effect: The cleaning cloth made of ultra-fine fibers. After scraping the dirt, the dirt will migrate outward along the capillary channel of the fiber, showing an internal peeling effect, so that the dirt will not remain in the wipe The surface of the cloth is clean, so it will not cause scratches on extremely delicate products.
Choice of clean cloth
01 Gram weight: Is the gram of the same fabric the same
02 Type and quality: superfine fiber has higher quality and polyester fiber is lower
03 Softness: the softer the better
04 Abrasion resistance: the stronger the fiber, the less fiber will be lost
Different edge banding methods of clean cloth
01 Laser cutting: Instantly melted by the laser at high temperature, the edge banding degree reaches 99%, no chips, no dust, and clean treatment such as net shower and cleaning can be done after cutting, so that the product can reach a higher dust-free standard. The disadvantage is that the edge is slightly hard because it is melted, and 75% of the market uses this edge sealing method;
02 Ultrasonic cutting: through the vibration generated by the ultrasonic vibration unit-vibrator, the electrical energy is converted into mechanical energy, and the heat is transferred through the welding head, and the fabric is squeezed by the tool. The edge banding degree is less than 80%, and the edge banding is better than laser edge banding. More soft and beautiful;
03 Cold cutting: Cut directly with electric scissors, without edge sealing. This cutting method is prone to produce lint on the edge, the technology and cost are the lowest, and it cannot be cleaned after cutting. During the wiping process, a certain amount of cloth debris will be generated on the edge , No cleanliness. Generally not recommended for high-end wiping;

Clean cloth classified by material
Dust-free cloth, the nickname in the industry is called wiping cloth, but also called purification cloth, cleaning cloth, etc. There are many names, but there are only the following types of products:
1. Quality choice-microfiber clean cloth
The superfine fiber dust-free cloth is made of polyester and nylon composite superfine long fiber woven satin. Using laser or ultrasonic cutting edge heat sealing technology, low dust, low ion precipitation, it is a commonly used cleaning cloth in tenth and hundredth class dust-free workshops. It has excellent water and oil absorption performance, very low ion residue and particle quantity, and is relatively general. Ester dust-free cloth has better softness and ability to prevent surface scratches. It is suitable for TFT-LCD, Wafer production lines and other environments with extremely high requirements for dust-free cloth.
2. High cost performance-imitating microfiber clean cloth
100% continuous polyester microfiber double woven, wear-resistant treatment, strong chemical resistance. Using laser or ultrasonic cutting edge heat sealing technology, effectively prevent the scattering of dust and fibers. It is suitable for the electronics industry, LCD/LED industry, optoelectronic industry and other environments with extremely high requirements for dust-free cloth. It is a substitute for low-demand microfiber cloth.
3. Economical universal cloth——Straight/Net-grain polyester wipe cloth
100% continuous polyester fiber knitting method into straight weave and net weave. Generally, laser or ultrasonic cutting edge heat sealing technology is used to effectively prevent the scattering of dust and fibers. It is suitable for semiconductors, hard disks, precision printing, PCB exposure rooms, small-size LCD bonding, residual glue, and dust-free workshops with large amounts of dirty liquid.
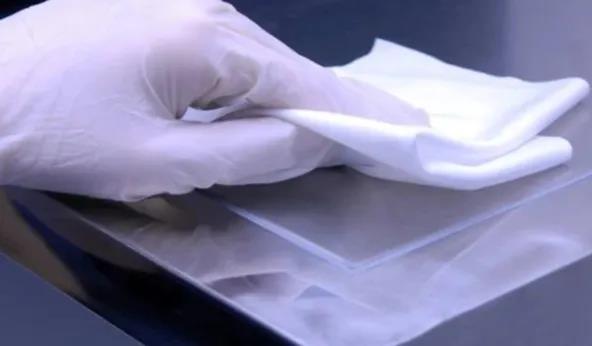