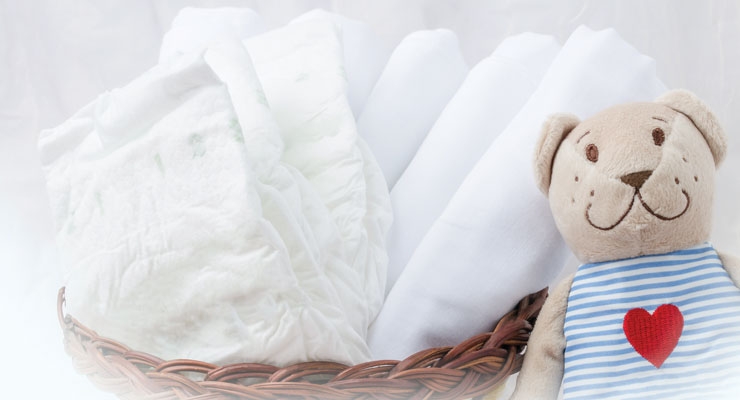
One of the world's largest non-woven technology, spunbond and fusible non-woven production technology, whether in its core market - the health market or other fields, not only in production but also in the scope of application continues to develop. Although many people think that the PP Spunbond market is equivalent to the health market, some experts say that slightly more of this type of non-woven fabric is used in industrial applications than in health (52%).
Many new lines have emerged around the world, especially those made by reicofil leffen, a German machine supplier, which provide the products with low weight, high strength and uniformity needed in today's health market. It almost represents the application standard of the sanitary material market. At the same time, leffin technology can also provide huge production capacity, so their equipment is regarded as the standard to build successful products in the health industry despite the high price.
'Spunbonded polypropylene continues to be a major technology platform in the non-woven business, particularly in the health sector,' said David price, an industry consultant. We see that due to the differences in market development, technology growth is faster in some parts of the world than in other regions. '
According to price, between 2010 and 2015, 37 new lines were put into operation in the world, many of which were invested in new factories in developing regions including India, Africa and the whole Asia Pacific region. Driven by improving the quality of health products, the capacity of these new production lines is expected to be fully utilized in many regions by 2020 or before.
Although the number of new line announcements has decreased in recent months, in the past year, all companies targeting the health market, including Berry Plastics in North America, pegas in the Czech Republic, FITESA in South Carolina and fibertex personal care in Malaysia, avgol in Israel and India, Toray advanced materials in South Korea, Mitsui in Japan Both chemical and Asahi Kasei in Thailand have new production lines. These production lines not only improve the output of health products, but also meet the changing demand of the market. For example, they can achieve the goal of lighter weight, softer feel and less consumption of raw materials, and to a certain extent, they replace the old production lines. These outdated technologies and production lines will be used in markets other than health materials.
Softer, softer
In recent years, many industry observers have been amazed by the Chinese diaper market, which has raised the softness standard to an unprecedented level. Due to the demand for softer diapers in China's diaper market, the rest of the world has followed suit and developed more value-oriented solutions. This trend has penetrated into the non-woven industry, forcing manufacturers to adjust their output to meet market demand.
Although some companies choose to increase their 'softness' by air bonding or carding (hot air process), others adjust their existing products through raw material changes or processing improvements to develop softer fusible materials.
Berry Plastics is probably the world's largest manufacturer of spunbonded and melt spun nonwovens, with a variety of production methods to provide softer nonwovens, and by investing in new carding technology to improve the production of its melt spun nonwovens. The company recently completed a $20 million carding line investment in Italy's terno d'isolata plant, which will help it launch high-end materials like 3D airten, which will improve the softness and fluffy to a new height, and have customizable three-dimensional texture patterns. This material, which will be launched next year, may be an extension of airten-22s, a high-quality hot-air non-woven fabric for surface and bottom layers.
Of course, berry Berry's spinning and melting business continues to maintain a strong momentum of development. In May 2016, the company announced that it would add a new line to an undisclosed address in North America. The new line will add 16000 metric tons of capacity to the company's existing North American base, including production lines in Virginia, North Carolina and Mexico (serving the North American market), and will focus on high-end applications in the health and healthcare markets.
This new line and other recent berry berry investments are likely to be related to a number of other new 'soft' products, including kamisoft advance, a soft non-woven fabric, and ng s-tex, which provide superior discernible softness. Berry berry will also upgrade its soft knurled roll product, which is located in nueville, France, and was purchased from dounor nonwovens a few years ago.
In terms of machinery, technology leader reicofil leffin has developed technology to meet the demand of non-woven fabrics for fluffy and soft, especially for surface and bottom applications, while the middle layer products are gradually squeezed out of the market by other high-quality materials.
Michael Maas, director of operations, research and development, said that in June 2016, the company launched a new development of high pile spunbond technology, which provides a unique possibility for manufacturing thick soft non-woven fabrics and has the potential to develop new application areas for its customers,
The technology of 3D non-woven fabric is developing continuously in reicofil technology center, which is the largest research and development center in the world, specializing in the production of spunbond nonwovens. Located in Troisdorf, Germany, the center has three high-tech product lines, working closely with customers, institutions and other partners to carry out research.
A large number of non-woven fabric production is usually composed of self crimped fibers, but reicofil technology uses two kinds of filaments of different raw materials to spray out through parallel structure, and uses hot air or special embossing roller to press together, to generate high-quality non-woven fabric material used as the bottom layer of the surface layer in the urine pants.
Reicofil sees another potential market for its high pile nonwovens as packaging for bulk items. The company's 'Rethinking packaging' project includes solutions for packaging bulk materials with non-woven fabrics. The team developed a prototype of non-woven cement bag. 'Imagine the potential of moving this solution to the non-woven market of packaging various bulk goods - the packaging industry,' Maas added. 'We are currently committed to replacing paper bags and woven polypropylene bags, thanks to our superior performance and irresistible price advantages.
Back in the health market, fibertex is one of the players who choose to upgrade their existing equipment to improve their softness. The Aalborg, Denmark based company announced the upgrade of its existing production line - reportedly with new spinneret capacity - which not only increased production capacity, but also enabled it to produce super soft melt non-woven fabrics comparable to its Malaysian plant, while the company's fifth line will be put into production at its second plant in Malaysia.
Avgol, an Israeli company, has also fine tuned its spunbond and fusing technologies to meet the needs of softer products. It is said that avgol lux series fabric provides manufacturers with a solution of visually unique soft touch fabric. These three products, including soft, silky soft and cotton soft, are suitable for the top, bottom and leg hoops, as well as the base materials of the waist and waist to meet the latest sanitary product design trends.
Executives said the new line, which has been developed for many years, represents significant research and development investment in many product performance parameters. The line was first launched in Asia. 'The demand for soft nonwovens that we see comes from China and is now spreading around the world is actually a challenge to the status quo and a driving force for new products,' price said. 'No matter what type of technology they use, this is a great opportunity for everyone in the non-woven business.
As the development of improved reicofil leffin technology continues to pave the way for advanced hygiene materials, old reicofil leffin technology, such as the reicofil leffin 3 production line installed in the 1990s and 2000s, has not been shut down. 'Instead, they are targeted at non health sectors such as the car or filter market because they provide a competitive cost structure,' price explains