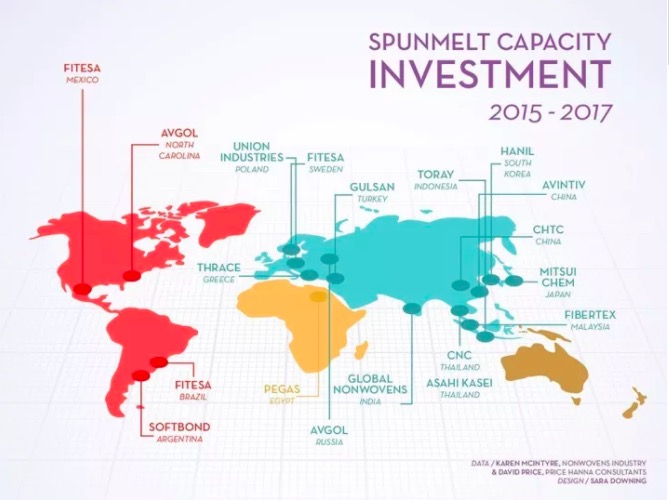
The strong demand for non-woven products has promoted the rapid growth of new non-woven lines and production capacity. According to the report from smtihers Pira, a market research company, in 2017, the global non-woven market totaled 10.1 million tons or 269.8 billion square meters, with us $42.3 billion, and is expected to reach 13.6 million tons, or 382 billion square meters and US $57.4 billion by 2022. The annual growth rate for the 2017-2022 period is expected to be 6.2% (tonnes), 7.2% (M2) and 6.3% (USD).
Although the global growth rate of non-woven fabrics remains at a healthy level of 6-7%, it is expected to decline slightly by 2022. The overall sustained growth in 2017-2022 but slight slowdown reflects lower than historical growth expectations in Asia (China), South America (Brazil) and parts of Europe.
According to the way of use, non-woven fabrics can be divided into two categories: disposable and durable. Disposable non-woven fabric is usually used for a relatively short time or single use, mainly used in consumer products, such as diapers, female health products, adult incontinence products and most wipes. Durable non-woven fabrics usually have a long service life or can be used many times, such as filter materials, car floor mats, mattress materials, Geotextiles in the road and weed control materials, which are only a part of durable non-woven products.
In recent years, the pace of non-woven production capacity growth has never slowed down, and throughout the world, the footprint of new lines is all over every continent. The main driving factors behind this are the increase of market demand and the update of equipment technology. Next, let's count each region's new non-woven lines and capacity growth one by one.
Asian region
The strong demand for disposable products, on the one hand, reflects the growing demand of the growing middle class in Asia for higher performance and higher value-added consumer goods, such as diapers and women's hygiene products, on the other hand, the market for washable wipes is growing.
In order to reflect the development potential of the market, some leading non-woven manufacturers are investing in new production lines in order to seize the opportunity and increase sales. At the same time, the new production line also provides manufacturers with the latest technology, which enables them to produce thinner and lighter materials, with lower production costs, to meet the 'light' demand for sanitary products.
Berry global will invest in one of the most advanced reicofil RF5 spinning fusion lines in Asia. According to reifenh ä user, RF5 can reduce the fiber diameter by 20%, so as to meet the growing market demand for microfiber.
The new line will provide an increase of 20000 tons for the Asian market, and this investment will help Berry to meet the growth of customer demand in the future health and special materials market. As for the best place to invest, berry is looking in China and is expected to start operations in 2019.
According to the statistics of CNITA middle class association, the growth rate of China's non-woven industry in 2016 was 13.87%, the investment reached 30.622 billion yuan, and the growth rate in the first quarter of 2017 reached 41.81%.
In 2016, China added 152 new non-woven production lines, 88 spunbond and fusible composite lines, 37 Spunlaced non-woven lines and 30 all cotton Spunlaced lines (according to the order contract).
Looking at the non-woven fabric market in Japan, the growth rate of domestic non-woven fabric production capacity is far lower than that of overseas market, because many Japanese manufacturers focus their investment on other regions of Asia.
Asahi Kasei Asahi, the leading enterprise in the direction of overseas investment, recently announced that it would increase its third line in Thailand and double its production capacity. Mitsui Mitsui, invested and produced 15000 tons in China and 30000 tons of new non-woven fabric line in Thailand. Other Japanese non-woven fabric manufacturers recently invested overseas, including daiwabo's four hot air lines in Indonesia and UNITA's 10000 ton polyester spunbond new line in Thailand.
In fact, Japanese non-woven enterprises continue to invest in Japan, but the growth rate is not as good as the overseas market. Misui just announced to expand its production capacity of spinning melt line in Japan, and unitika also announced to upgrade its existing production facilities.
The following table shows the domestic and overseas production of Japanese non-woven manufacturers.
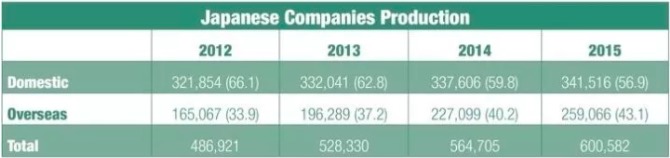
The overseas production of Japanese non-woven enterprises increased by 30000 tons every year from 2012 to 2015, from 165000 tons to 259000 tons. The gross domestic product and overseas production in 2012 totaled 486900 tons, 528330 tons in 2013, 564705 tons in 2014 and 600000 tons in 2015, with an average annual growth rate of 6-8%.
The growth of overseas production increased from 33.9% in 2012 to 43.1% in 2015. Thanks to the continuous investment of Japanese enterprises, the total overseas production is expected to exceed the domestic production in 2018-2019.
Most of the overseas production lines are spinning fusion lines, accounting for about 70%. According to the use of finished products, health care accounted for 78.7% of overseas production in 2015.
India's non-woven production began in the 1970s, in the early stage, it was limited to the use of staple fibers produced by conventional methods to make non-woven fabrics. In 996, two Indian nonwovens companies began to produce PP Spunbond Nonwovens, both of which introduced reifenhauser reicofil technology from Germany, and were the forerunners of Fiberweb and unimin.
The original idea of Indian society is that products can be cleaned and used repeatedly, but not accepted to use disposable products. But with the rise of local labor costs, the use of disposable products began to become cheap and convenient, so the disposable non-woven industry began to grow.
With the development of automobile, geotextile and filter industry, the market of needle punched non-woven fabric is also growing. In the past 15 years, there have been many different types of non-woven fabrics in India, and the growth is amazing.
In 2016, India produced 365000 tons of non-woven fabrics, an increase of 17% over the previous year. Most of the current production is used in low-end markets, such as shopping bags, carpets and linings. However, with the continuous growth of automobile, filter, geotextile and medical and health industries, the industry is also developing to the high-end market. At the same time, the imported products made of non-woven fabrics will also be replaced by the local manufacturing industry in India.
As early as 2009, Ahlstrom invested 42 million euros in Mundra Special Economic Zone (SEZ) in the Indian special economic zone (SEZ) to establish a 12000 ton annual production capacity spinning fusion line. Last year, avgol also announced that it would invest 2.23 billion rupees in the mandideep area to build a new line.
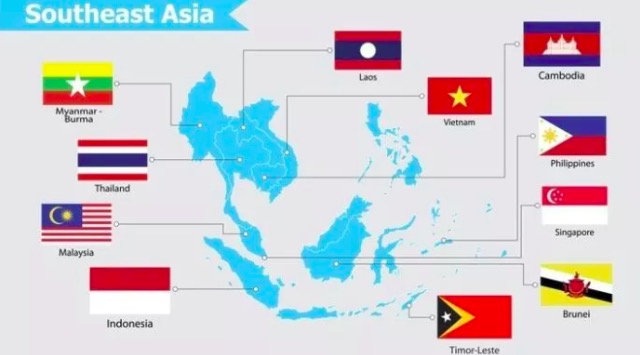
According to the forecast, the production capacity and market demand (intraregional demand and export) of non-woven fabrics in Southeast Asia will continue to grow during 2016-2020, with an average of 5.5-6%, slowing down compared with the growth rate of 8-10% in 2010-2015.
However, demand will continue to grow as the market penetration of disposable and durable non-woven fabrics in Southeast Asia, Asia Pacific and China's export markets remains low. Sanitary products are the largest market of non-woven fabric processing industry, followed by durable geotextile and its related uses.
In 2017, the production capacity of non-woven fabrics in Southeast Asia mainly focused on spunbond ultra fine denier technology, followed by staple fiber carding and needling, hot rolling and spunbond polypropylene needling technology.
According to the announced or ongoing capacity expansion, the capacity of polypropylene spunbond technology in the region is expected to increase from 193000 tons in 2015 to 263000 tons in 2018, accounting for 6% of the global total capacity of polypropylene spunbond at that time.
Malaysia accounts for 35% of the total capacity in Southeast Asia, or 79000 tons. Indonesia accounts for 14% of the total capacity, about 32000 tons.
The largest non-woven fabric manufacturers in Southeast Asia all adopt super fine denier polypropylene spunbond / melt technology, focusing on the health market. According to the forecast, by 2020, the production capacity of super fine and medium denier spunbond and melting in Southeast Asia will reach 263000 tons, of which 114000 tons or 43% are from Thailand, 97000 tons or 37% from Malaysia and 52000 tons or 20% from Indonesia. 35% of them are from fibertex.
The capacity of Asahi and CNC in Thailand is close to 40000 tons in 2016. The two companies have completed their recent expansion and have yet to announce further investment plans. Mitsui (Thailand) and Dongli (Indonesia) both put into production 30000 tons of spinning and melting production lines in 2016. Toray's capacity will increase to 40000 tons in 2017. Mitsui may not continue to expand in Southeast Asia until 2020, as their new production line invested in Japan will be put into operation in mid-2018.
Ten Cate is the only medium denier polypropylene spunbond non-woven fabric manufacturer in Southeast Asia. It supplies the geotextile market and other related industries through acupuncture process. Since 1996, the production capacity has remained unchanged at 9000 tons / year.
European Region
In fact, berry is not the first company to have a new line of RF5. Gulsan company from Turkey announced its investment plan in Turkey in the first half of the year. One line is RF5, six die head, 5.2m wide, which can provide 35000 tons of production capacity and serve the health and medical market. It is believed that after the production line is put into production, it will become a sample line of reifenhauser leffin in Germany, so as to show more potential customers the technology and capabilities of RF5.
According to data provided by Edana, the non-woven fabric production in Europe reached 2.38 million tons in 2016. Despite the impact of the economic climate, it still increased by 2.5%, showing the continuous development momentum of the industry. The growth rate of EU countries is higher than the average growth rate of the whole Europe, and the growth rate of some of them is particularly eye-catching.
Germany, Italy and Spain grew at a higher rate, with Spain even reaching 5%, which compensated for the decline in the rest of the region.
In terms of industry, the health market accounts for 30.7% (tons) of the total output, but the agricultural and clothing industries have reached double-digit growth, with air filtration, construction and food and beverage industries growing at 3.2%, 4.5% and 4.25% respectively. In contrast, the auto industry is down 1%. The medical and personal care market remained basically stable, down slightly by 0.4%.
Berry Plastics has installed a new carding line at its plant in teneodora, Italy, to launch new products in the health market. In addition to its earlier investment in Norrk ö Ping, Sweden, FITESA launched a new spinning fuse in peine, Germany, in early 2017. Suominen has also made some investment upgrades in Spain to increase its market share in industrial wipes and medical non-woven fabrics.
American region
According to Inda's report, North America added 8 new lines in 2015, and by 2016, the number of new lines reached 17, while the forecast for 2017 was 14 (still increasing), among which 3 were applied to the filtration industry.
In recent years, Sandler from Germany, norafin, mogul from Turkey and uniquetex from China have successively invested in the United States. Berry also announced that he would invest in a new line in the United States, at which time he would launch softer fabrics.
On March 23 this year, tenowo, a German company, held a ribbon cutting ceremony in Lincoln, North Carolina, USA, to celebrate the completion of its US $12.5 million expansion project of machinery and plant facilities, making tenowo's total investment in the region more than US $25 million since 2000.
Glatflter plans to invest $80 million in Fort Smith, Arkansas, to produce air laid nonwovens, which are expected to start production by the end of 2017 or early 2018.
FITESA completed its new line investment in Cosmo ó polis in Brazil and Jos é Iturbide in Mexico in 2016. It is likely that it will invest in a new line in Simpsonville, South Carolina in 2019.
At the same time, suominen's large production line in Bethune, South Carolina will be completed soon, which will focus on the growing market of washable wipes. In Brazil, suominen also intends to expand its product portfolio with the aim of strengthening its position in the South American market, especially in the medical and health non-woven market.
Looking at so many new lines in the world, the entrepreneurs in China's non-woven industry must have been full of blood. They need to visit all over the world and choose the best investment destination.